A vast number of service providers express work management steps with planning and scheduling alone. Unfortunately these steps only cover a small portion of the entire work management lifecycle necessary for an organization to adequately address asset-based issues correctly and in a timely fashion. At CAMS we focus on the entire process from the point of the customer voicing an issue (work identification) through to the analysis, reporting, and actionable feedback phases. Our approach helps to ensure complete coverage of all elements of the process along with servicing as a catalyst for continuous improvement.
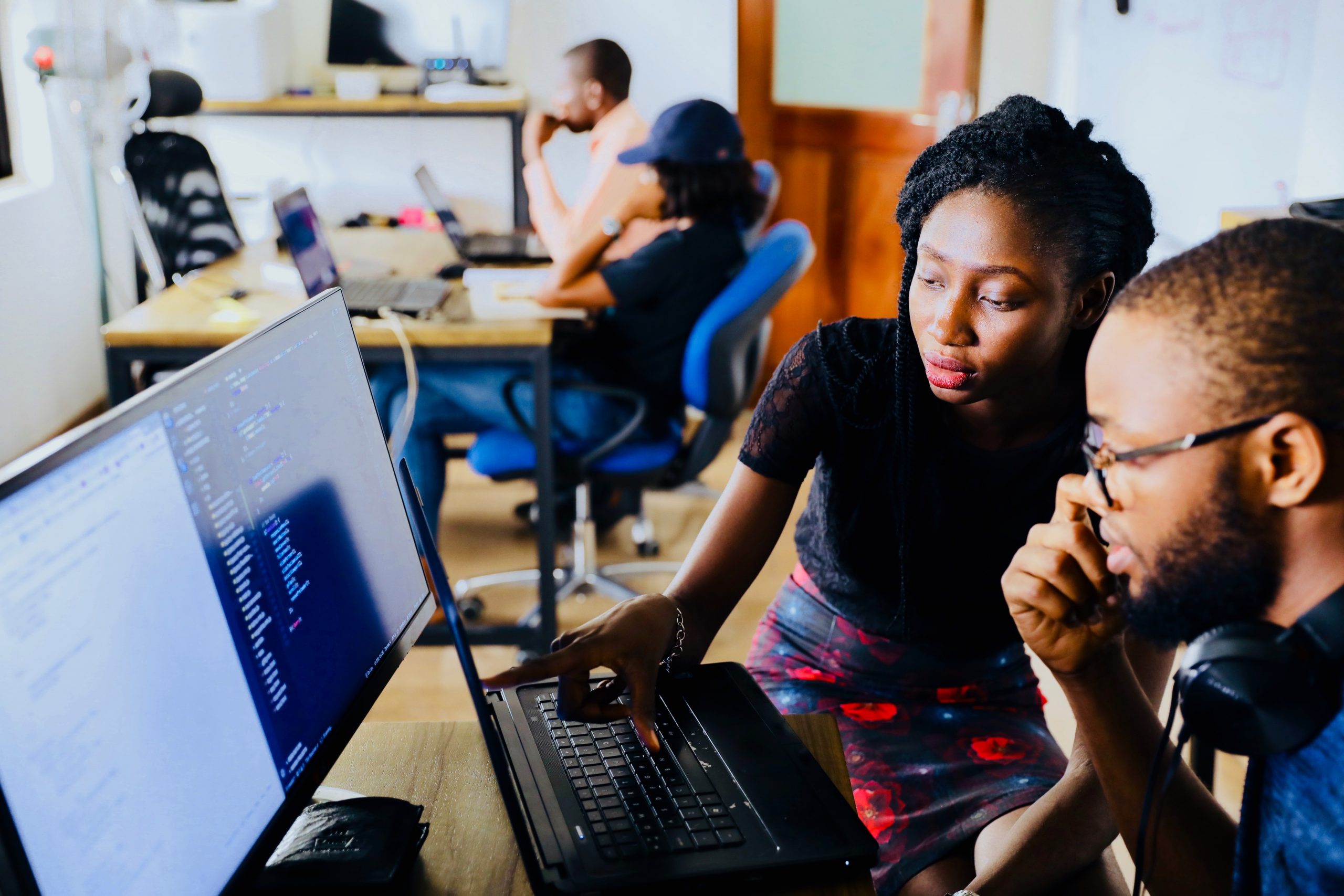
Work Identification & Review
CAMS Consulting utilizes all available means to ensure proper work identification is made for any deficiencies, equipment improvements and other work that requires attention. We work with our clients to develop, train, and implement means to get these work requests into your company’s EAM/CMMS system. It is critical to obtain accurate and concise information at the time or work request; as a result CAMS ensures that key information is captured to ensure prompt response is achieved to remedy problem and avoid re-work due to poor data capture.
As important as identification of work needed is, CAMS knows it is critical to ensure the organization has a planned response to handle these requests for decision and next actions. Review of the data by stakeholders for priority, possible duplication, need date for repair, and response to emergent work are critical success factors for an organization’s asset utilization and reliability. CAMS works with clients to design and implement for deciding on immediate next actions for all incoming work.
Planning
Planning is a vast array of steps, interdependencies, and requirements that should be viewed in its own right separate from and prior to the scheduling activities. CAMS Consulting works in various modes (design/development, implementation, coaching) to ensure that the client’s Planners are equipped with the proper knowledge, skills and abilities to plan maintenance activities for the facility. For both preventive and routine repair maintenance, we work with our clients to implement thorough, stored job tasks with all requisite data (i.e. crafts, estimated hours, materials/tools, permits, etc) to increase the efficiency of job preparations for the next phase in the workflow.
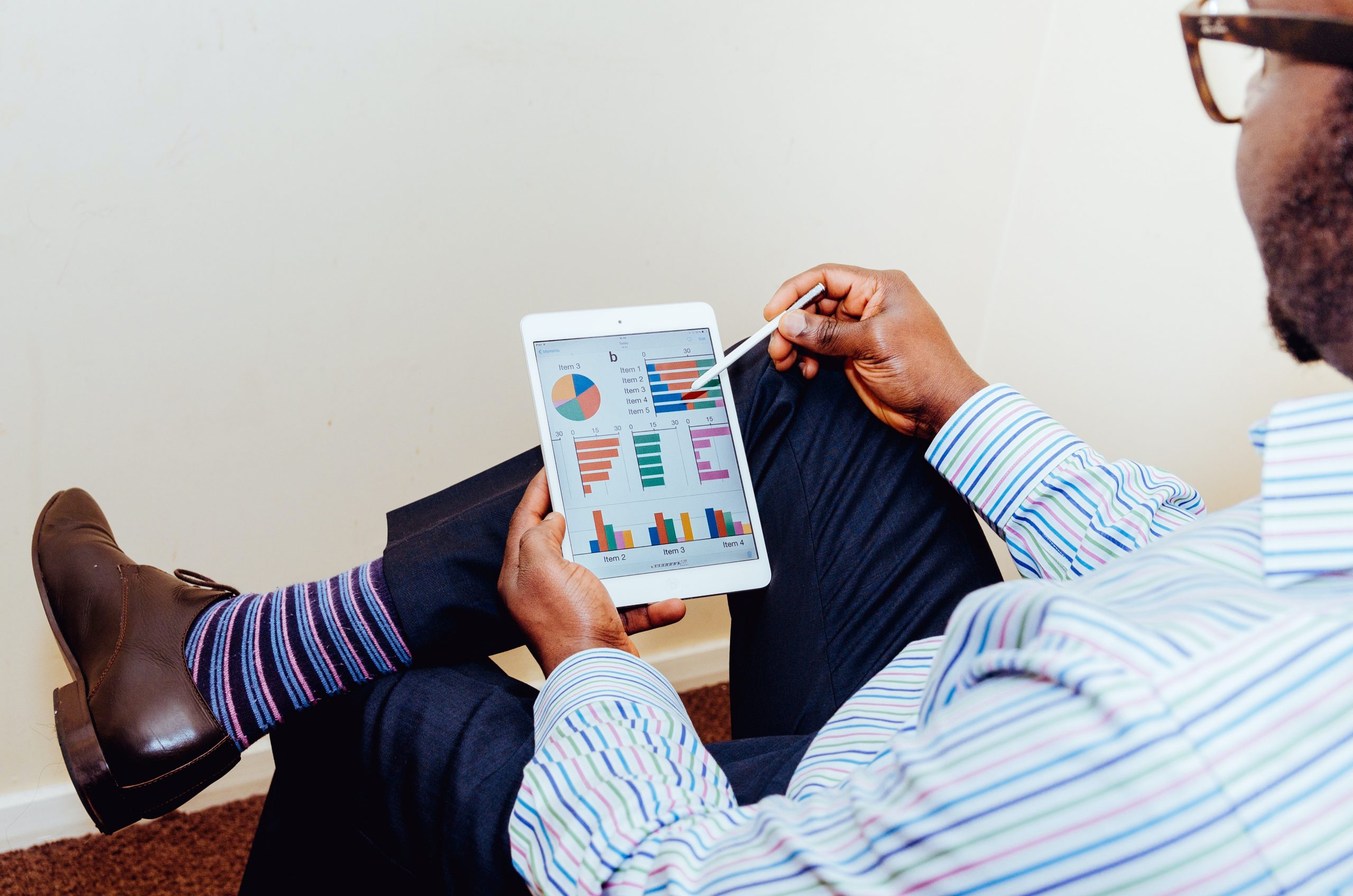
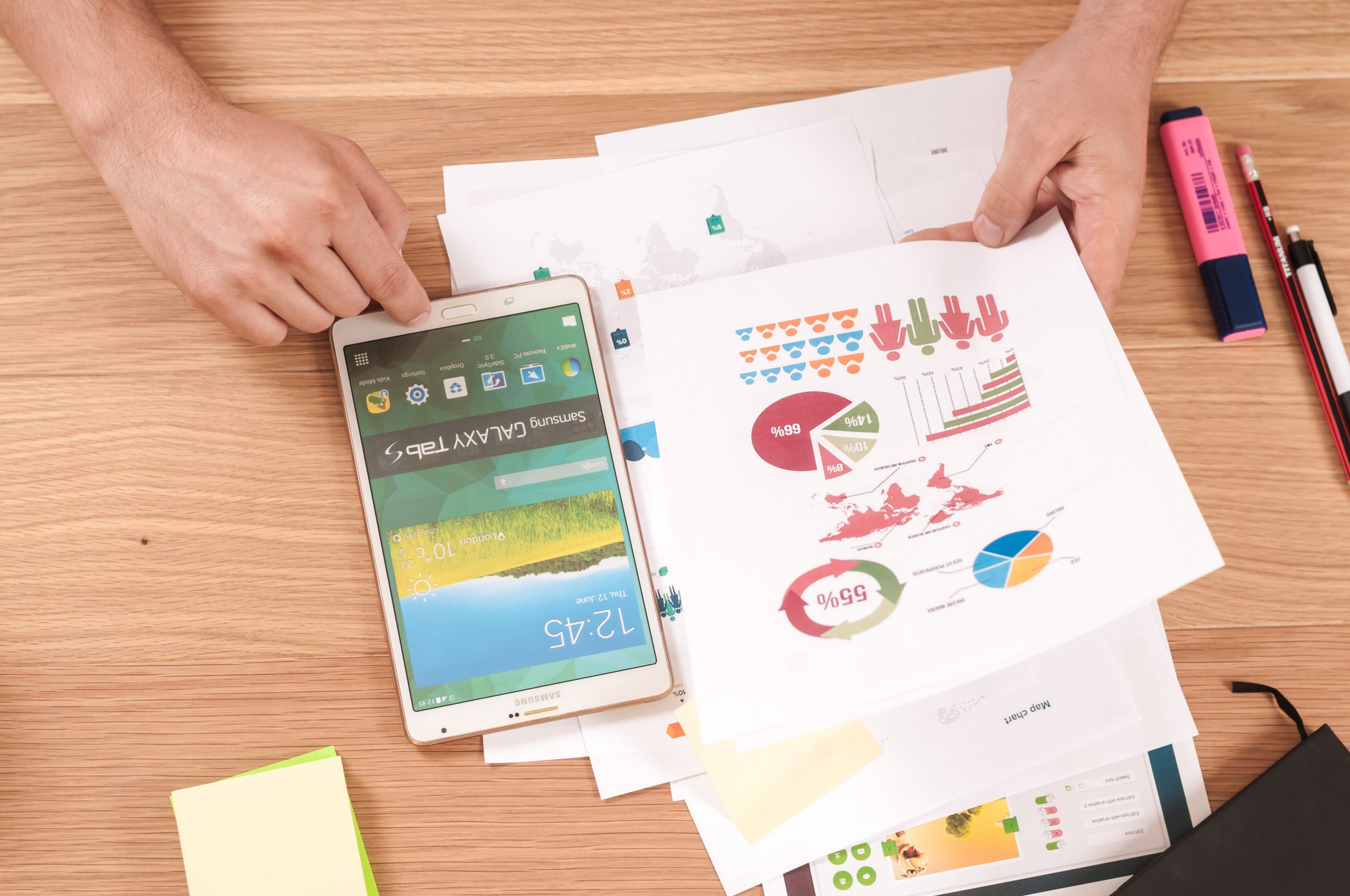
Scheduling
Creating cohesive, accurate and timely schedules is a critical step in the work lifecycle process of each job. As such, CAMS Consulting works with the scheduling resources and involved parties to make sure sure the right work is scheduled for the right time on the right assets by:
- Creating a maintenance and operations asset partnership agreement
- Integrating production forecasts with maintenance activities required
- Ensuring collaboration meetings take place for equipment availability assurance
- Performing work package readiness prior to entering the scheduling queue
- Conducting long and short-term scheduling review sessions
- Coaching applied scheduling optimization techniques and methods
- Developing a long-term scheduling horizon program
- Coaching load-leveling of resources and workload for near and long term planning
Work Closeout
As important as getting the job is, it is equally critical that actuarial information is captured for valuable work history, reliability improvements, and overall continuous improvement. CAMS Consulting will work with your Performing Technicians to ensure they have simple, clear and efficient means for capture of this valuable information into your Asset Information System database (EAM/CMMS). We are experienced in a vast array of widely used systems so that we can effectively perform both classroom and hands-on training with each technician. We strive and have achieved sustainable results in this area by sufficiently promoting the importance of information to all members of the organization.

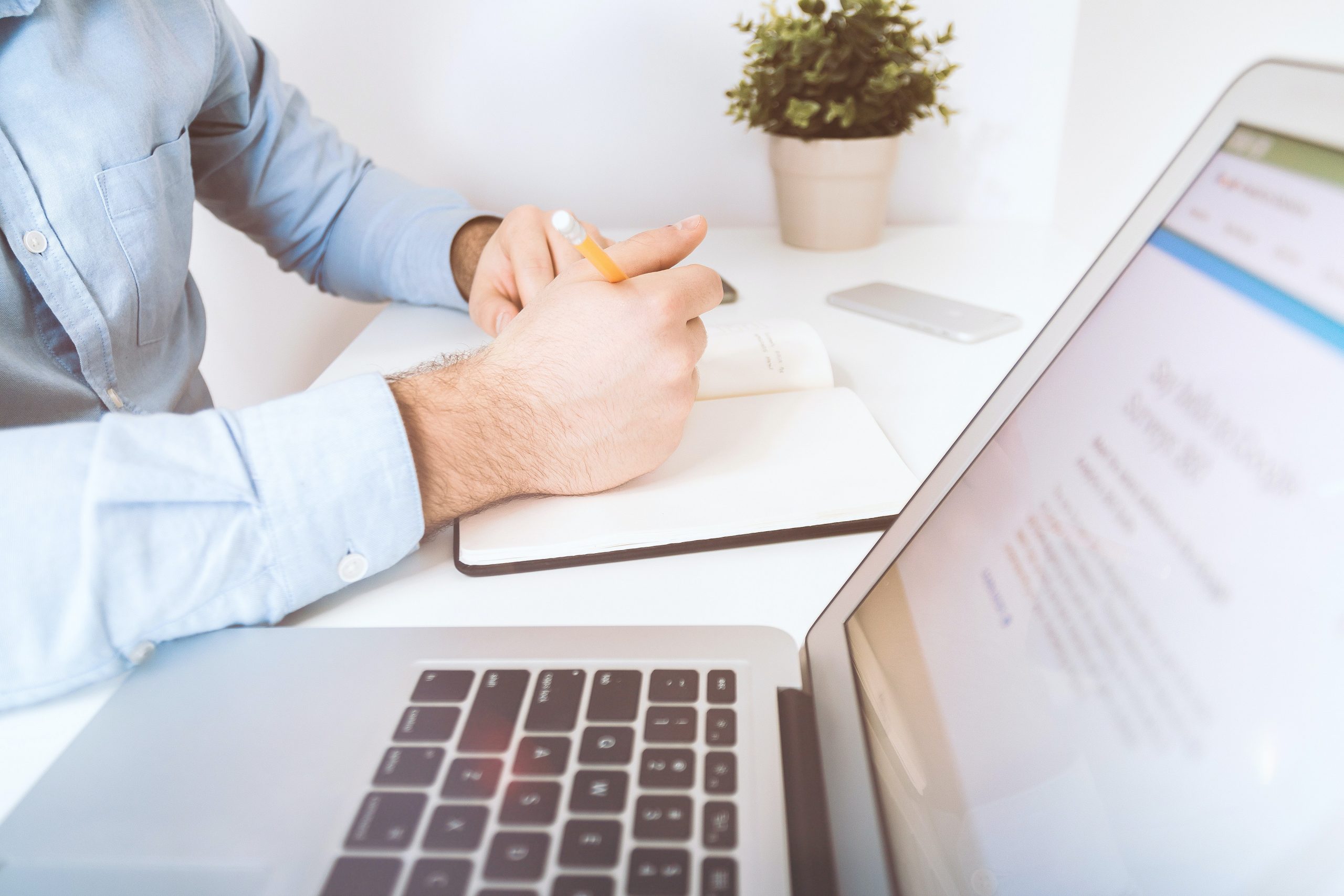
Work Feedback Loop
CAMS Consulting utilizes the Plan-Do-Check-Act (PDCA) in all aspects of our working engagement with each organization. The PDCA Loop is a vital process in ensuring the work identified, planned, scheduled, executed and documented feed into the continuous improvement initiatives your organization has or desires. We train managers, technicians, operators and reliability engineers how to extract data for meaningful use and improvement of your assets and business processes. In addition we work with your resources to create timely, useful, and actionable reports within or external to your EAM/CMMS systems. Many organizations get lost in the ‘paralysis by analysis’ phase at this point by looking at too many supposed performance indicators. We at CAMS instead focus on what’s key to driving your business from a reliability and asset management perspective to spend more time on the ‘doing’ of improvement.